Leveraging Buoyancy for Enhanced Heat Transfer in Plate Type Heat Exchangers
- Protap Sarker
- Feb 6, 2024
- 2 min read
Introduction:
In the dynamic world of industrial processes, even a subtle modification in equipment design can yield significant improvements. Recently, our plant experienced a noteworthy enhancement in heat transfer efficiency through a strategic adjustment in the heat exchanger configuration. The modification involved reversing the hot oil flow direction in a plate type heat exchanger, leading to a remarkable boost in heat transfer rates. This transformation was primarily attributed to the buoyancy effect, a phenomenon that played a pivotal role in optimizing the heat exchange process.
Understanding Plate Type Heat Exchangers:
Plate type heat exchangers have been a staple in industrial settings due to their compact design, efficiency, and versatility. The fundamental principle involves the exchange of heat between two fluids separated by metal plates. The heat transfer occurs through conduction across the plates and convection between the fluids.
Historical Flow Configuration:
In the initial setup, our hot oil entered from the top and exited from the bottom of the heat exchanger in a cross-flow pattern. This conventional arrangement served its purpose, but innovation beckoned us to explore potential improvements.
Modification and Flow Reversal:
The recent modification involved a simple yet strategic change: redirecting the hot oil flow from the bottom, allowing it to exit from the top. This adjustment, driven by an understanding of fluid dynamics and buoyancy, resulted in a paradigm shift in heat transfer dynamics.
Buoyancy Effect and its Impact:
Buoyancy, the upward force exerted by a fluid on a submerged object, is a crucial factor in the improved performance of our heat exchanger. By introducing hot oil from the bottom, we capitalized on the natural buoyancy of the fluid, creating a buoyant force that facilitated a more effective circulation and mixing of the fluids within the heat exchanger channels.
Enhanced Heat Transfer Mechanism:
The buoyancy effect induced a more vigorous and efficient mixing of hot and cold fluids, breaking down boundary layers and promoting increased convective heat transfer. This phenomenon led to a substantial reduction in thermal resistance and a consequent rise in heat transfer rates.
Benefits of the Modified Configuration:
Improved overall heat transfer efficiency
Reduced energy consumption
Enhanced temperature uniformity across the exchanger
Minimized fouling and scaling due to improved fluid circulation
Conclusion:
The modification in our plate type heat exchanger, guided by a strategic understanding of buoyancy effects, exemplifies the potential for innovation in industrial processes. By harnessing natural forces, we have significantly improved heat transfer rates, underscoring the importance of fluid dynamics in optimizing thermal performance. This case study serves as a testament to the continuous pursuit of efficiency and sustainability in industrial operations.
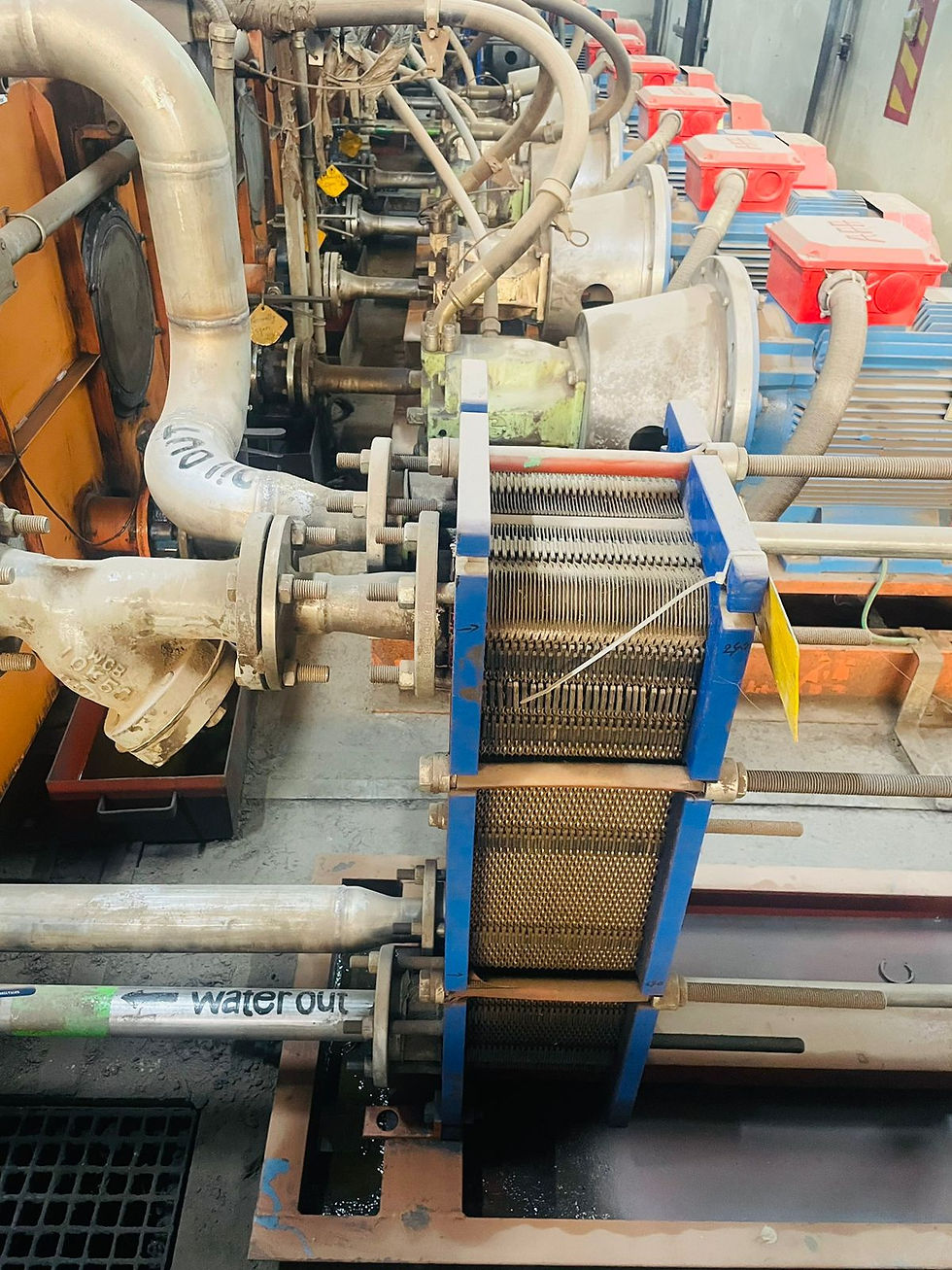
Comments